Unlocking the Secrets of a Compressor Air End: A Comprehensive Guide
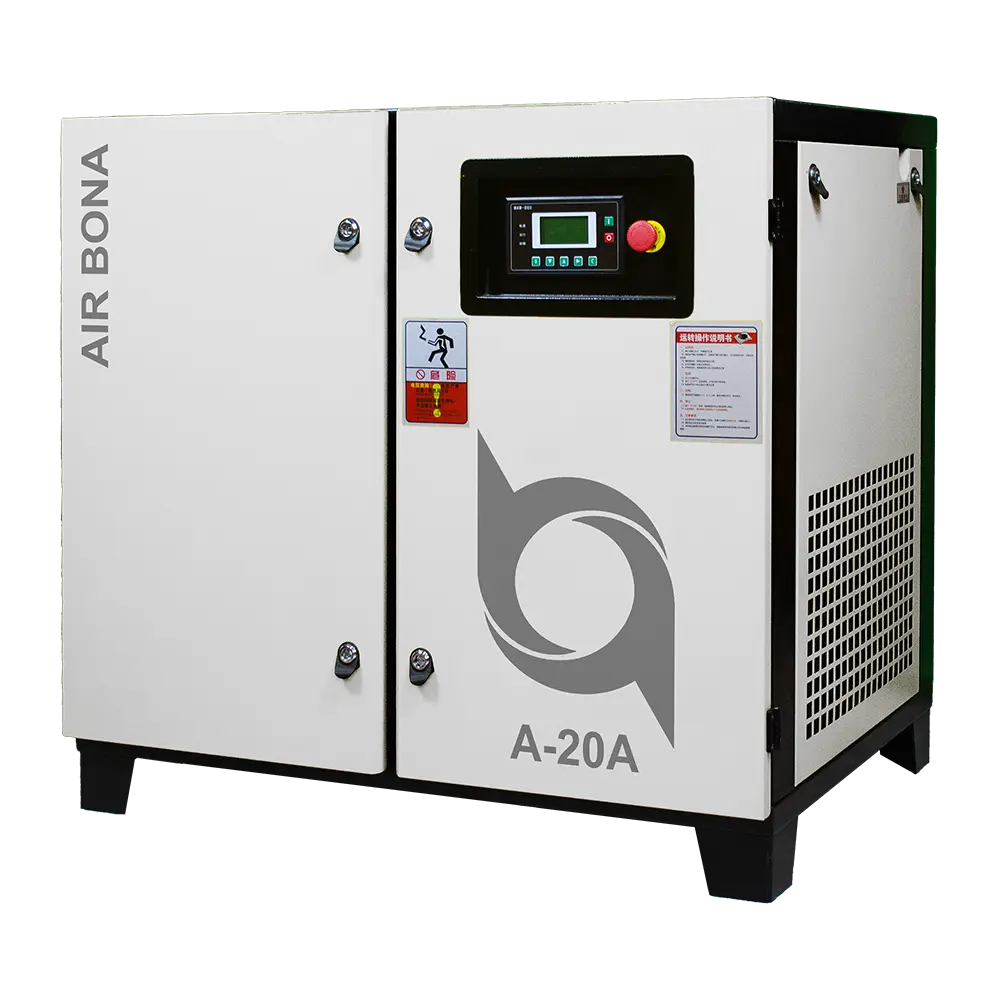
Are you curious about how a compressor air end works? Look no further! In this comprehensive guide, we will unveil the secrets behind the inner workings of a compressor air end. Whether you are new to the world of compressors or an experienced professional seeking a deeper understanding, this article is for you.
From the fundamental principles to the intricate components, we will delve into every aspect of a compressor air end. Learn about the various types of compressors, the role of the air end, and how it converts power into compressed air. We will also explore the key factors that affect the performance and efficiency of an air end, helping you select the most suitable equipment for your needs.
With our expert insights and industry knowledge, you’ll gain a clear understanding of the compressor air end and its crucial role in various applications. Get ready to unlock the secrets and master the essentials of compressor technology.
Let’s embark on this enlightening journey and develop a deeper appreciation for the fascinating world of compressor air ends.
Importance of a compressor air end
The compressor air end is the heart of any compressor system. It is responsible for converting mechanical power into compressed air, which is essential for various industrial applications. Without a properly functioning air end, the entire compressor system would be rendered useless.
The significance of a compressor air end lies in its ability to generate compressed air efficiently and reliably. By understanding the importance of this component, you can ensure that your compressor system operates at its optimal level, maximizing productivity and minimizing downtime. A well-maintained air end can also contribute to energy savings and reduce operational costs.
In the next section, we will explore the components that make up a compressor air end and how they work together to produce compressed air.
Components of a compressor air end
A compressor air end consists of several key components that work in harmony to generate compressed air. These components include the compressor pump, air filters, intercooler, aftercooler, oil separator, and discharge valves.
The compressor pump is the main component of the air end and is responsible for compressing the air. It typically consists of a rotor, stator, and a series of vanes or screws. As the rotor rotates, it creates a pressure differential, which results in the compression of air.
Air filters are crucial in removing contaminants and impurities from the intake air before it enters the compressor pump. They help prevent damage to the pump and ensure the production of clean, high-quality compressed air.
The intercooler and aftercooler play a vital role in cooling the compressed air. The intercooler cools the air between stages of compression, while the aftercooler cools the air before it is delivered to the end-use application. Cooling the compressed air helps increase its density and improves the efficiency of the system.
The oil separator is responsible for removing oil from the compressed air. It ensures that the air delivered is free from oil contamination, which is crucial for applications that require oil-free air, such as food processing or pharmaceutical industries.
Lastly, the discharge valves control the flow of compressed air from the air end to the downstream system. They ensure that the air is delivered at the desired pressure and regulate the system’s overall performance.
Understanding the role and function of each component is essential for troubleshooting and maintaining a compressor air end. In the next section, we will explore the working principles of a compressor air end in more detail.
Understanding the working principles of a compressor air end
The working principles of a compressor air end depend on the type of compressor technology used. The most common types are reciprocating compressors, rotary screw compressors, and centrifugal compressors.
Reciprocating compressors use a piston and cylinder arrangement to compress air. As the piston moves inside the cylinder, it creates a vacuum, drawing air into the cylinder. The piston then compresses the air, which is discharged through the air end.
Rotary screw compressors utilize a pair of interlocking helical screws to compress air. As the screws rotate, the air is trapped between the threads and compressed as it moves towards the discharge end.
Centrifugal compressors use centrifugal force to compress air. A high-speed impeller accelerates the air, creating a high-pressure zone. The air is then discharged through the air end at the desired pressure.
Regardless of the type of compressor, the air end’s main function is to convert mechanical power into compressed air. This process involves compressing the air, cooling it, and removing any contaminants before it is delivered to the downstream system.
In the next section, we will explore the different types of compressor air ends and their respective advantages and limitations.
Types of compressor air ends
There are various types of compressor air ends available, each with its advantages and limitations. The choice of air end depends on factors such as the desired pressure range, flow rate, and application requirements.
Reciprocating air ends are best suited for applications that require high-pressure air and intermittent operation. They are known for their durability and ability to deliver high-quality compressed air. However, they can be noisy and require more maintenance compared to other types of air ends.
Rotary screw air ends are widely used in industrial applications due to their high efficiency, reliability, and continuous operation. They are capable of providing a steady supply of compressed air at various pressure ranges. However, they are generally not suitable for high-pressure applications.
Centrifugal air ends are ideal for large-scale industrial applications that require high flow rates and very high-pressure ratios. They offer excellent efficiency and reliability but are more complex and expensive compared to other types of air ends.
Choosing the right air end for your needs requires careful consideration of factors such as pressure requirements, flow rate, energy efficiency, and maintenance requirements. Consulting with a compressor expert can help you make an informed decision.
In the next section, we will discuss common issues that can arise with a compressor air end and how to troubleshoot them.
Common issues and troubleshooting techniques for a compressor air end
Like any mechanical system, a compressor air end can experience issues that affect its performance and efficiency. Some common problems include air leaks, excessive heat, oil contamination, and inadequate pressure.
Air leaks can result in a loss of compressed air, leading to decreased efficiency and increased energy consumption. To troubleshoot air leaks, inspect the system for damaged hoses, fittings, or seals. Repair or replace any faulty components to restore the integrity of the system.
Excessive heat can be caused by factors such as inadequate cooling, dirty coolers, or worn-out components. To resolve heat-related issues, ensure that the cooling system is functioning properly and clean or replace any dirty or damaged coolers. Additionally, inspect the compressor pump for any worn-out parts that may be contributing to excessive heat generation.
Oil contamination can occur when the oil separator fails to remove oil from the compressed air. This can lead to issues such as clogged filters, decreased air quality, and damage to downstream equipment. Regularly check and replace the oil separator to prevent oil contamination.
Inadequate pressure can be caused by factors such as worn-out valves, incorrect pressure settings, or leaks in the system. Check the discharge valves for proper operation and adjust the pressure settings as needed. Inspect the system for any leaks and repair them promptly to maintain the desired pressure.
Regular maintenance and monitoring of the compressor air end can help prevent issues and ensure optimal performance. In the next section, we will discuss maintenance and care tips for a compressor air end.
Maintenance and care for a compressor air end
Proper maintenance and care are essential for ensuring the longevity and performance of a compressor air end. Here are some tips to help you maintain your air end:
- Regularly inspect and clean the air filters to prevent the buildup of contaminants that can affect air quality and system performance.
- Monitor the oil level and quality to ensure proper lubrication of the compressor pump. Regularly change the oil and replace the oil filter as recommended by the manufacturer.
- Keep the coolers clean and free from debris to maintain optimal cooling efficiency. Regularly inspect the coolers for any signs of damage or leaks.
- Check the discharge valves for proper operation and adjust as needed to maintain the desired pressure.
- Monitor the system for any abnormal sounds, vibrations, or performance issues. Address any problems promptly to prevent further damage.
- Follow the manufacturer’s recommended maintenance schedule and guidelines for your specific air end model.
By following these maintenance and care tips, you can ensure that your compressor air end operates at its best and prolong its lifespan. In the next section, we will explore upgrades and improvements that can enhance the performance and efficiency of a compressor air end.
Upgrades and improvements for a compressor air end
Technology advancements have paved the way for various upgrades and improvements that can enhance the performance and efficiency of a compressor air end. Here are some examples of upgrades and improvements you can consider:
- Variable speed drive (VSD) technology allows the compressor to match the air demand by adjusting the motor speed. This results in energy savings and improved efficiency.
- Upgrading to energy-efficient motors can further reduce energy consumption and operating costs.
- Implementing remote monitoring and control systems allows for real-time monitoring of the air end’s performance, enabling proactive maintenance and troubleshooting.
- Consider upgrading to a more advanced air end model that offers improved efficiency, lower maintenance requirements, and increased reliability.
- Implementing a compressed air management system can help optimize the overall efficiency and performance of the compressor system.
When considering upgrades and improvements, consult with a compressor expert to determine the most suitable options for your specific needs and budget.
In the next section, we will discuss the factors to consider when choosing the right compressor air end for your needs.
Choosing the right compressor air end for your needs
Choosing the right compressor air end requires careful consideration of various factors. Here are some key factors to keep in mind:
- Pressure requirements: Determine the required pressure range for your application. Consider both the minimum and maximum pressure needed.
- Flow rate: Calculate the required flow rate to ensure that the air end can meet your specific needs.
- Energy efficiency: Look for air ends that offer high energy efficiency ratings to minimize operating costs.
- Maintenance requirements: Consider the maintenance requirements of the air end, including oil changes, filter replacements, and overall system care.
- Reliability and durability: Choose an air end that is known for its reliability and durability, as this will minimize downtime and maintenance costs.
- Application-specific requirements: Consider any specific requirements of your application, such as the need for oil-free air or special environmental conditions.
By considering these factors, you can make an informed decision and choose the right compressor air end that meets your specific needs.
Conclusion: Optimizing performance and efficiency with a compressor air end
In conclusion, understanding the secrets behind a compressor air end is essential for optimizing the performance and efficiency of your compressor system. By delving into the components, working principles, and types of air ends, you can make informed decisions when selecting, maintaining, and upgrading your air end.
Regular maintenance and care, along with troubleshooting techniques, can help prevent issues and ensure optimal performance. By choosing the right air end for your needs and considering upgrades and improvements, you can further enhance the efficiency and reliability of your compressor system.
Unlocking the secrets of a compressor air end is a journey that requires continuous learning and adaptation. With our comprehensive guide, you now have the knowledge and insights to master the essentials of compressor technology. Embrace this knowledge and unlock the full potential of your compressor air end.
Happy compressing!