Unlocking the Mysteries of Air Compressor Unloader Valves: Your Definitive Guide
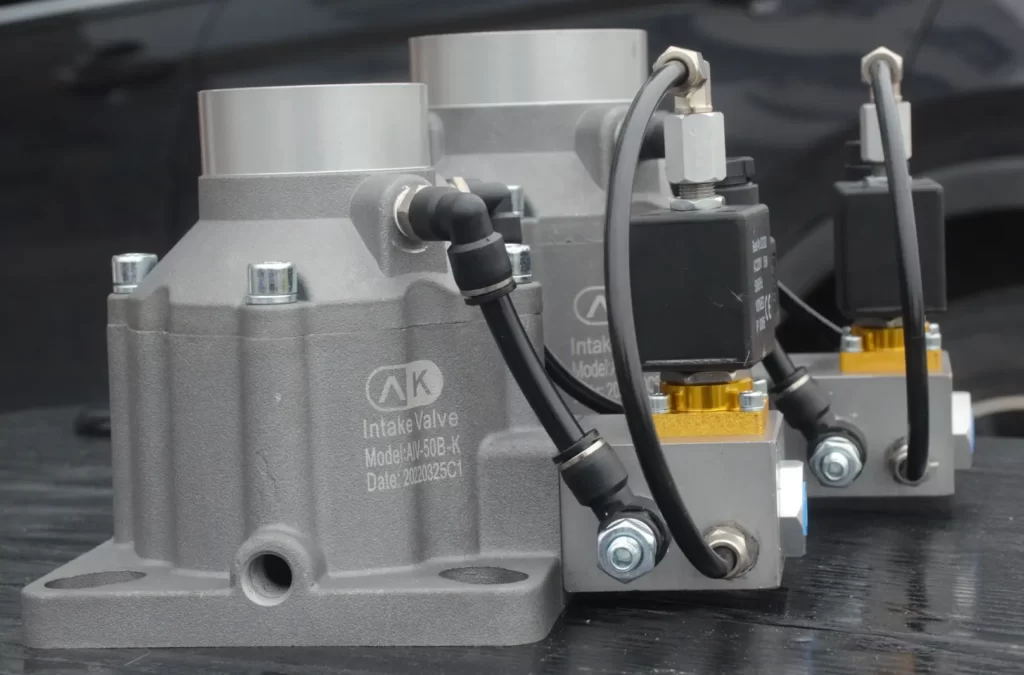
If you’re seeking clarity on the subject of air compressor unloader valves, your search ends here. In this all-encompassing guide, we’ll demystify everything you need to know about these vital components. Whether you’re an experienced technician or new to air compressors, grasping the concept of unloader valves is crucial for optimizing your compressor’s performance.
We’ll unravel the technical jargon surrounding unloader valves, delve into their functions, and explore the various types available. From explaining how unloader valves regulate pressure to troubleshooting common problems, this guide serves as your go-to resource for mastering these integral parts.
So, if you’ve ever found yourself puzzled by unloader valves, consider this your roadmap to clarity. By the end of this guide, you’ll have a confident understanding of air compressor unloader valves, enabling you to make informed maintenance decisions and keep your compressor operating at its peak.
Understanding the Role of Air Compressor Unloader Valves
Air compressor unloader valves play a critical role in the overall operation of a compressor. These valves are designed to release pressure from the compressor’s discharge line when the compressor stops. This action prevents the compressor from starting under load, which can strain the motor and other components. Additionally, unloader valves reduce the starting torque required, extending the motor’s life and improving efficiency.
Unloader valves are particularly crucial in reciprocating air compressors, ensuring that the compressor starts with no load, minimizing wear on the motor and drive components. Understanding the significance of unloader valves helps users appreciate their role in maintaining the compressor’s longevity and performance.
Furthermore, unloader valves contribute to energy efficiency by relieving excess pressure during the compressor’s unload cycle, preventing unnecessary power consumption. This underscores the importance of understanding and maintaining these valves to optimize the overall energy efficiency of the air compressor system.
Types of Air Compressor Unloader Valves
Air compressor unloader valves come in various types, each serving specific purposes and applications. One common type is the constant speed unloader valve, which unloads the compressor at a fixed pressure level. This type is suitable for applications requiring a consistent pressure level, such as certain industrial processes and equipment.
Another type is the load/unload unloader valve, which unloads the compressor when the pressure reaches a predetermined level and reloads it when the pressure drops to a set threshold. This type of unloader valve is commonly used in applications with varying pressure demands, enabling efficient and adaptable compressor operation.
Additionally, there are modulating unloader valves that provide precise pressure control by continuously adjusting the compressor’s capacity based on the system’s air demand. These valves are ideal for applications with fluctuating air usage, contributing to precise pressure control and energy savings.
Understanding the distinctions between these types of unloader valves empowers users to select the most suitable option for their specific air compressor system, considering factors like operational requirements, energy efficiency goals, and environmental considerations.
How Air Compressor Unloader Valves Work
To understand how an air compressor unloader valve operates, it’s essential to grasp the underlying principles of its functionality. When the compressor reaches the unload phase, the unloader valve releases the pressure trapped in the compressor’s discharge line, allowing the compressor to start without working against the built-up pressure. This process prevents motor strain and reduces the power required for the compressor to restart.
In reciprocating air compressors, the unloader valve is typically actuated by the pressure switch, which senses the tank’s pressure and controls the compressor’s operation. When the pressure switch detects that the predetermined pressure level has been reached, it activates the unloader valve to release the trapped pressure, ensuring a smooth start for the compressor during the next cycle.
For rotary screw compressors, the unloader valve functions slightly differently. These compressors use a pneumatic or electronic control system to adjust the compressor’s capacity, including unloading it when necessary to maintain optimal operation. Understanding the specific unloading mechanisms of different compressor types is crucial for effective maintenance and troubleshooting of these components.
By comprehending the inner workings of air compressor unloader valves, users gain insight into the coordination between the compressor, pressure switch, and unloader valve, enabling them to diagnose potential issues and optimize the performance of the entire air compressor system.
Common Issues with Air Compressor Unloader Valves
While air compressor unloader valves are essential for proper compressor operation, they can experience issues that affect performance and efficiency. One common problem is the failure of the unloader valve to release pressure during the unload cycle, causing the compressor to start under load. This can lead to motor strain and increased energy consumption, highlighting the importance of promptly addressing malfunctioning unloader valves.
Furthermore, unloader valves may develop leaks, allowing air to escape even when the compressor is not running. These leaks result in pressure loss in the system, affecting overall performance and potentially causing the compressor to cycle more frequently to maintain the desired pressure levels. Identifying and fixing such leaks is vital for preserving the efficiency and longevity of the air compressor.
Another prevalent issue involves unloader valves getting stuck in either the open or closed position, hindering their ability to regulate pressure effectively during the compressor’s operation. This can lead to irregular pressure levels and erratic compressor behavior, requiring thorough inspection and potential replacement of the affected valves.
By recognizing these common issues with air compressor unloader valves, users can proactively address maintenance and repair needs, ensuring consistent and reliable performance of their air compressor systems.
Troubleshooting and Maintenance of Air Compressor Unloader Valves
Proper maintenance and troubleshooting of air compressor unloader valves are indispensable for preserving their functionality and optimizing compressor performance. Regular inspection of the valves, including visual checks for leaks and physical assessments of their operation, is a fundamental aspect of maintenance.
In the event of malfunctioning unloader valves, troubleshooting may involve testing the valve’s actuation mechanism, verifying the pressure switch’s functionality, and inspecting the pneumatic or electronic control systems for any irregularities. Additionally, cleaning and lubricating the unloader valves can help prevent sticking and ensure smooth operation.
It’s imperative to follow the manufacturer’s maintenance guidelines and recommended service intervals for the unloader valves to prevent premature wear and potential failures. This may include replacing worn seals, diaphragms, or other components to maintain the integrity of the valves and prevent performance degradation.
By incorporating a comprehensive maintenance regimen and systematic troubleshooting approach, users can mitigate potential issues with air compressor unloader valves and uphold the reliability and efficiency of their compressor systems.
The Importance of Proper Adjustment and Settings
Optimal performance of air compressor unloader valves relies on proper adjustment and settings tailored to the specific application and operational requirements. Adjusting the unloader valve’s set pressure, which determines the pressure level at which the valve unloads the compressor, is critical for aligning the compressor’s operation with the system’s demands.
Furthermore, ensuring that the unloader valve is synchronized with the pressure switch or control system is essential for seamless operation and efficient pressure regulation. Misalignment between these components can lead to irregular compressor cycling, excessive pressure fluctuations, and increased energy consumption, underscoring the significance of precise adjustment and synchronization.
Moreover, verifying that the unloader valve’s settings correspond to the compressor’s capacity and the system’s air demand is vital for maintaining optimal performance and energy efficiency. Proper adjustment and settings of the unloader valve contribute to stable pressure control, reduced wear on compressor components, and minimized energy consumption, ultimately enhancing the overall reliability and longevity of the air compressor system.
Upgrading to a More Efficient Unloader Valve
As advancements in air compressor technology continue to evolve, upgrading to a more efficient unloader valve can yield significant benefits in terms of energy savings and performance optimization. Modern unloader valve designs may incorporate enhanced control algorithms, precision modulation capabilities, and advanced materials to improve reliability and efficiency.
For users seeking to maximize energy efficiency and operational flexibility, upgrading to a modulating unloader valve equipped with intelligent control features can offer precise pressure regulation, adaptability to varying air demand, and reduced energy consumption. This upgrade can result in substantial cost savings and environmental benefits, making it a compelling option for users aiming to elevate the efficiency of their air compressor systems.
Additionally, upgrading to a more reliable and durable unloader valve can contribute to an extended service life and reduced maintenance requirements, further enhancing the overall cost-effectiveness and operational resilience of the air compressor. Evaluating the potential gains from upgrading to a more efficient unloader valve can lead to long-term advantages in performance, energy savings, and sustainability.
Safety Precautions and Best Practices
When working with air compressor unloader valves, observing safety precautions and adhering to best practices is paramount to prevent accidents and ensure optimal system performance. Before conducting maintenance or adjustments on unloader valves, it’s crucial to depressurize the air compressor system and follow appropriate lockout/tagout procedures to eliminate potential hazards.
Furthermore, using personal protective equipment, such as safety glasses and gloves, when handling unloader valves can safeguard against injury and exposure to compressed air. Following the manufacturer’s guidelines for maintenance, adjustment, and troubleshooting procedures is essential for maintaining a safe working environment and preserving the integrity of the air compressor system.
Regular training and education on safe practices related to air compressor maintenance and operation can cultivate a culture of awareness and responsibility among personnel involved in the care of these systems. By prioritizing safety precautions and best practices, users can mitigate risks and uphold a secure and efficient working environment conducive to optimal air compressor performance.
Choosing the Right Air Compressor Unloader Valve for Your Needs
Selecting the right air compressor unloader valve tailored to specific application requirements and operational parameters is critical for achieving optimal performance and efficiency. Factors to consider when choosing an unloader valve include the type of compressor, the system’s air demand profile, pressure regulation needs, and energy efficiency objectives.
For applications with varying air demand and fluctuating pressure requirements, a load/unload or modulating unloader valve may offer the adaptability and precision control necessary to optimize compressor operation and energy consumption. Conversely, applications with consistent pressure demands may benefit from a constant speed unloader valve, providing stable pressure regulation and reliable performance.
Furthermore, evaluating the compatibility of the unloader valve with the existing compressor system, including the pressure switch, control mechanisms, and safety features, is vital for seamless integration and reliable operation. Consulting with experienced professionals or manufacturers can provide valuable insights into selecting the most suitable unloader valve for specific operational needs and performance expectations.
By making an informed decision when choosing an air compressor unloader valve, users can align their system with the requisite pressure control, energy efficiency, and operational reliability, setting the stage for optimized compressor performance and longevity.
Conclusion
In conclusion, understanding air compressor unloader valves is essential for maintaining the efficiency, reliability, and longevity of air compressor systems. By comprehending the role, types, operation, maintenance, and safety considerations associated with unloader valves, users can make informed decisions to optimize their compressor performance and energy efficiency.
As technological advancements continue to drive innovation in air compressor technology, the significance of selecting the right unloader valve and incorporating best practices for maintenance and operation cannot be overstated. By staying informed about the latest developments and best practices in unloader valve management, users can elevate the performance and sustainability of their air compressor systems, ensuring seamless operation and energy savings for years to come.
Incorporating the insights and recommendations outlined in this guide can empower users to navigate the complexities of air compressor unloader valves with confidence, enabling them to proactively address maintenance needs, select the most suitable valve for their applications, and uphold a safe and efficient working environment. With a comprehensive understanding of air compressor unloader valves, users are poised to unlock the full potential of their air compressor systems and achieve lasting performance benefits.