Understanding The Functions and Working Principles of Rotary Screw Air Compressor Components
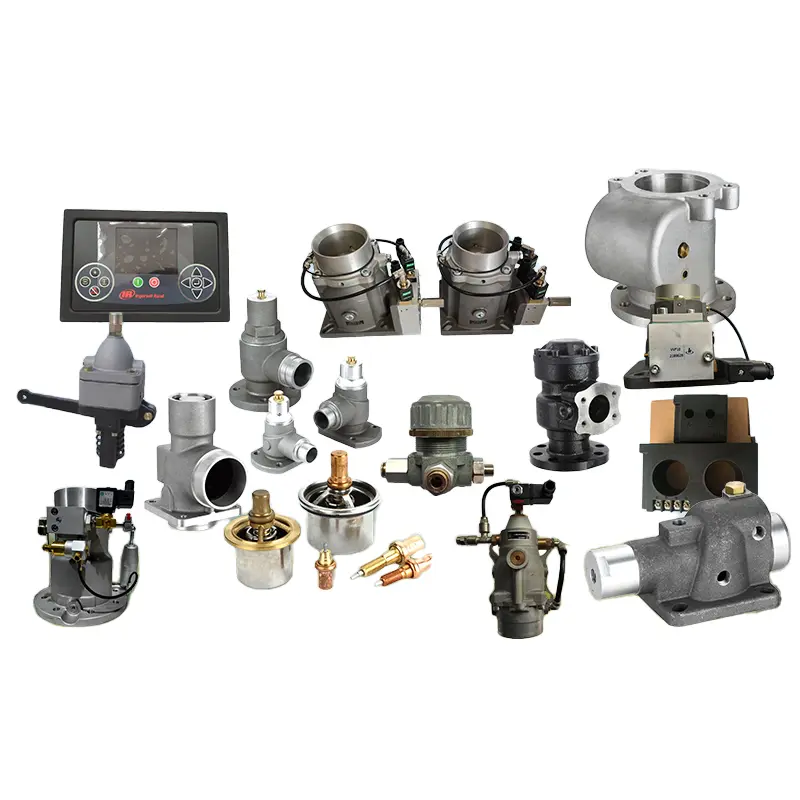
Rotary screw air compressors are a marvel of engineering, offering impressive performance and efficiency in a compact package. To appreciate the sophistication of these devices, we’ll delve into the function and operational principles of its key components.
Airend: This component, also known as the compressor element, is the heart of the machine. Two interlocking rotors or screws are housed within the airend. When these screws rotate, the air is trapped and compressed, then sent downstream for further processing.
Intake Valve: The intake valve regulates the volume of ambient air entering the airend. It opens and closes in response to system demand. In low demand periods, it restricts airflow to prevent over-compression, thereby conserving energy.
Motor: This provides the mechanical power to drive the airend. Most compressors use electric motors, renowned for their efficiency and reliability. They convert electrical energy into mechanical energy, causing the airend’s rotors to turn.
Oil Filter: A crucial part of any oil-injected rotary screw air compressor, the oil filter removes contaminants from the oil circuit, ensuring clean oil lubricates and cools the airend and other components. This extends the lifespan of the compressor.
Air Filter: The air filter purifies the incoming air, ensuring it’s free from dust, dirt, and other particulates. This prevents damage to the airend and maintains the quality of compressed air.
Separator Tank: After compression, air and oil mixtures pass into the separator tank. Here, the oil is efficiently separated from the air. The separated oil is recycled back into the system, while the air proceeds to the discharge system.
Fan: The fan is responsible for maintaining an optimal operating temperature. It cools the compressor by forcing ambient air through the cooler, preventing overheating that could lead to system damage.
Exchanger (Cooler): After exiting the separator tank, the compressed air often needs cooling. The exchanger, or cooler, uses a series of fins and tubes to dissipate heat from the compressed air, ensuring it’s at a suitable temperature for downstream use.
Controller: This digital device optimizes compressor operation by monitoring system conditions and adjusting compressor parameters accordingly. It controls start/stop operations, protects against system faults, and provides vital information on system health.
Coupling: The coupling connects the motor to the airend, allowing the motor’s mechanical power to drive the airend’s rotors. It’s designed to handle the power transfer efficiently while reducing vibration and noise.
Contactor: Lastly, the contactor is a switch controlled by the controller. It starts or stops the flow of electricity to the motor, thereby controlling the compressor’s operation.
Each component of a rotary screw air compressor serves an essential purpose, and together they form a machine that effectively converts ambient air into high-pressure air, ready for use in various industrial applications. Understanding these parts and their functions is critical in ensuring optimal operation and maintenance of your compressor.