The Critical Role of Precision Filters in Screw Compressor Systems
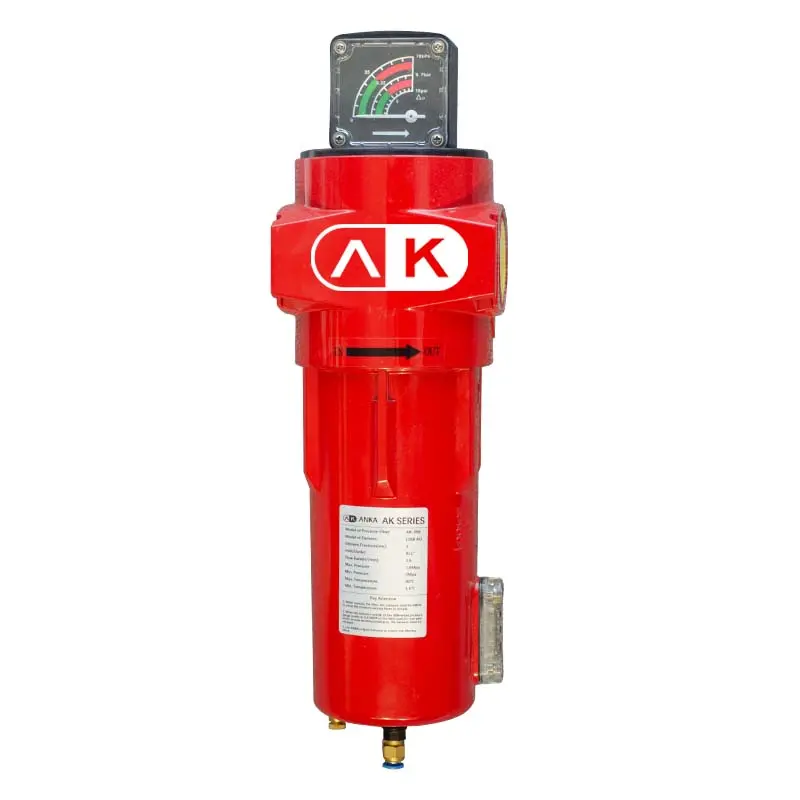
As the industrial domain progresses, the need for dependable, high-performance, and economical equipment grows more pressing. The screw compressor system serves as an essential apparatus, responsible for supplying compressed air to a range of applications. To preserve the system’s performance and stability, precision filters have emerged as vital elements. In this article, we will delve into the significance of precision filters within screw compressor systems and their contribution to the effective and seamless functioning of the entire system.
Understanding Screw Compressor Systems in Section 1
In the industrial sector, screw compressors are frequently used to compress air and transform mechanical energy into potential energy. Because to their great efficiency, dependability, and minimal maintenance needs, they are the favored option for many applications. These systems consist of two primary components: the screw compressor unit itself and the compressed air treatment system.
The compressed air generated by the screw compressor is typically mixed with contaminants, such as oil, water, and dust. These impurities may result in decreased performance, system outages, and even possible harm to delicate machinery. Precision filters serve as a crucial first line of defense in this situation, ensuring the caliber of the compressed air.
Section 2: The Significance of Precise Filters in Screw Compressor Systems
- Protecting the equipment: Precision filters remove contaminants from the compressed air stream, safeguarding downstream equipment from potential damage. The machinery’s lifespan is increased and maintenance expenses are decreased thanks to this protection.
- Improving system performance: Precision filters help screw compressor systems run as efficiently as possible by removing impurities from compressed air. Cleaner air leads to improved performance and reduced energy consumption, resulting in cost savings for the business.
- Ensuring product quality: In industries where compressed air is used for manufacturing, packaging, or other processes, the quality of the final product can be significantly impacted by contaminants in the air. Precision filters ensure that the compressed air is free from impurities, leading to better product quality and reduced chances of product recalls or rejections.
- Complying with industry standards: Many industries have strict regulations and standards for the quality of compressed air used in their processes. Precision filters help businesses meet these requirements, ensuring compliance and avoiding fines or penalties.
- Enhancing workplace safety: Contaminated compressed air can pose health concerns to employees and contribute to a hazardous working environment. Precision filters help maintain a cleaner and safer workplace by removing harmful contaminants from the air.
Section 3: Types of Precision Filters in Screw Compressor Systems
Different types of precision filters are used in screw compressor systems to target specific contaminants. Some of the most common filter types include:
- Particulate filters: These filters remove solid particles, such as dust and dirt, from the compressed air. They are essential for protecting downstream equipment and ensuring product quality.
- Coalescing filters: Designed to remove liquid contaminants, such as oil and water, coalescing filters capture and separate these impurities from the air stream.
- Activated carbon filters: These filters are specifically designed to remove gaseous contaminants, such as volatile organic compounds (VOCs) and odors, by adsorbing them onto a porous carbon surface.
- Sterile filters: In applications where sterile air is required, such as in the food, beverage, and pharmaceutical industries, sterile filters are used to remove bacteria, viruses, and other microorganisms from the compressed air.
Section 4: Proper Maintenance of Precision Filters
To ensure the ongoing efficiency and reliability of screw compressor systems, it is crucial to perform regular maintenance on precision filters. Proper maintenance practices include:
- Periodic inspection: Regularly inspect the filters for signs of wear, damage, or clogging. This will help identify any issues before they lead to system downtime or decreased performance.
- Filter replacement: Follow the manufacturer’s recommended replacement schedule for each type of filter. This ensures optimal filtration performance and extends the life of downstream equipment.
- Cleaning and maintenance: Some filters, such as reusable particulate filters, require periodic cleaning to maintain their effectiveness. Be sure to follow the manufacturer’s guidelines for cleaning and maintenance procedures.
- Monitoring filter performance: Keep an eye on filter performance indicators, such as pressure drop and air quality. These can provide valuable insight into the filter’s effectiveness and help determine when replacement or maintenance is needed.
Conclusion: Precision filters play a crucial role in the efficient and reliable operation of screw compressor systems. By removing contaminants from the compressed air, they protect downstream equipment, enhance system performance, ensure product quality, and maintain a safe working environment. By understanding the importance of precision filters and following proper maintenance practices, businesses can maximize the benefits of their screw compressor systems, ultimately leading to increased productivity and cost savings.